Tel. +91 9884195557 / 8610758878 | terrafirma.info@gmail.com
I-Bubble Reactor
THE PERFECT REPLACEMENT FOR CONVENTIONAL PRIMARY & SECONDARY TREATMENT
I-Bubble Reactor (IBR) Process is an extremely powerful emerging technology that is slated to completely re-define the way impurity is removed from waste water.
IBR completely replaces conventional physic-chemical precipitation, oil & grease removal, clarification process for addressing TSS, O/G, Turbidity
IBR completely replaces conventional biological treatment based on any technology (extended aeration, SBR, MBBR, MBR, FAB, RBC… ) for addressing COD & BOD
IBR is based on the principle of ELECTROLYTIC DEGRADATION of impurity.
Electrolytic Process is capable of removing the following
BOD,COD in sewage and effluents
Tss, Turbidity, oil & Grease in sewage and effluents
organics & even bio stable compounds
Soaps, detergents, laundry wastes
Iron & dissolved silica in raw water & R.O rejects
Arsenic & Flouride in raw waters
Paint, Pigments, Dyes
Heavy metal viz.. Chromium,Zinc,nickel
Oil & grease, Turbidity
Phenol, Formaldehye
Electrolytic Process Cannot remove Mono Valent ions in the water
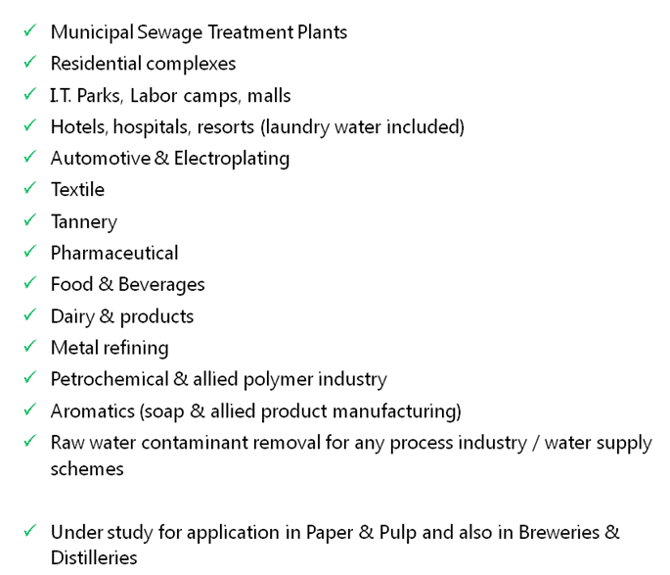
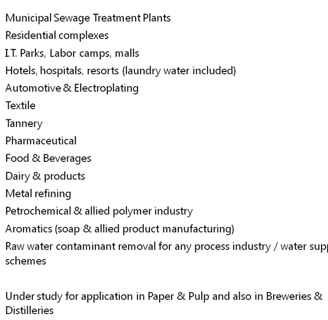
IBR PROCESS CAN BE USED EITHER AS AN “INSERTION MODEL” IN EXISTING TREATMENT PLANTS OR AS AN ALTERNATIVE TO CONVENTIONAL PROCESSES
Benefits:
Can operate at any % of the design capacity. Your 100 KLD plant can run even for 5 KLD. So, depending on the load, you can operate the plant. This is impossible in biological treatment wherein you need minimum 40% of the flow to even start the plant.
The Plant can be “switched on” and “switched off” at your convenience. This is impossible in biological process. Even if low flow or no flow is there, you have keep running the blower to maintain the bio mass. Else, the process has to be re-started, which will take time, money and effort.
Does not need any skilled operator to handle the plant. The plant can be easily maintained by even unskilled persons.
No noise in the treatment plant. In biological systems, the blower noise is a major nuisance, which is totally avoided in this system.
One of the major problems in bio process is the SMELL. This is significantly reduced in this process. There is practically no smell nuisance.
Bio process solids are very difficult to handle. This process does not generate bio sludge. The process generates solids which are hydro phobic and can be easily separated from the main water. Thus, dewatering is a very simple process.
Can degrade high concentration of impurity and complex organics in one step.
Start up and Shut down are immediate i.e within 1 hour. In bio process, it will take days to do the same activity
Any break down can be re-started in 1 hour to a maximum of 1 day. Biological treatment needs a minimum of 15 days to re-start in case of process break down.
Far lesser foot print area
Can be located anywhere in the area allotted.
IBR – Basic Principle:
In IBR process, the core process is BOND ENERGY DESTABILIZATION & DEPOLARIZATION of the organics, through electrolysis - passage of current
Organics + Current …> carbon ash + H2
Current is the driving force.
The heart of the treatment is the IBR REACTOR. Simplistically, the reactor containing the four elements viz.. ANODE, CATHODE, ELECTROLYTE & CURRENT bring about the destruction of organics through the process of electrolysis followed by Electro coagulation, floatation and removal of suspended impurity.
Every non bio stable compound exhibits bond energy. When the force applied is greater than the bond energy, there is break down of the compound. Bond energy destabilization happens in the cell and the organics are broken down into carbon ash and hydrogen gas. Destruction of organics takes place through bond depolarization. The dissolved impurity is thus converted to suspended impurity and volatiles go as gases.
So, in this process, the DISSOLVED impurity is broken down and converted to SUSPENDED impurity and gases. Once broken down, this suspended impurity is removed from the system by coagulation, floatation and subsequent precipitation.
The anode is in Aluminum and this dissolves in the water. Aluminum hydroxide is formed due to the electrolysis process. This acts as a powerful coagulant and brings all the suspended particles “together”. This process is called Electro Coagulation and this takes places simultaneously in the reactor
This coagulated mass is FLOATED UP the reactor and removed as scum. This process is called Electro Floatation. In E-KID process, hydrogen is generated in the cathode and this aids the floatation. In addition, floatation zone is created in the reactor.
This process is called Electro Floatation and this ensures that most of the suspended particles, oil and grease are removed as scum from the top of the reactor
The process is a combination of three unit operations occurring in a single reactor in one time zone – Electrolysis + Electro Floatation + Electro coagulation
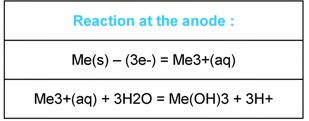
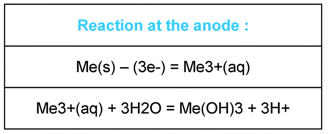
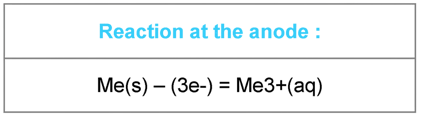
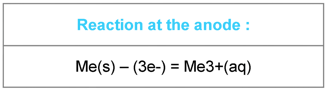
IBR Process– Typical Schematic
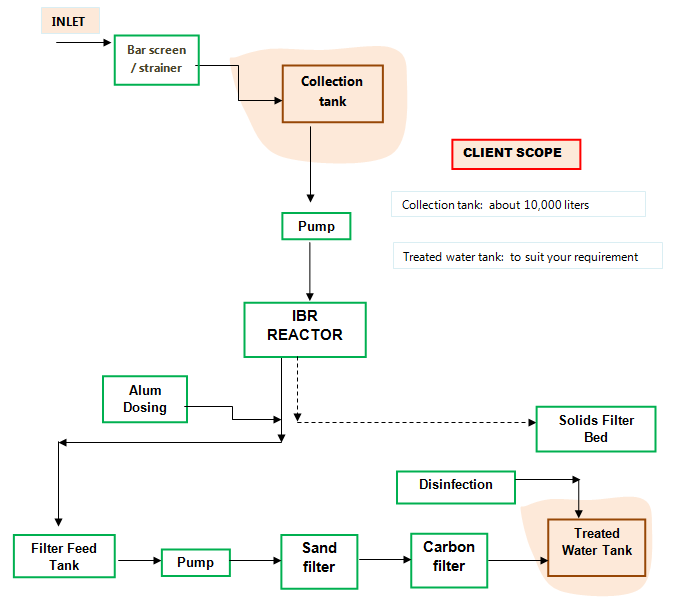
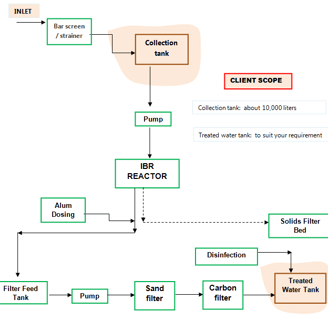
CONTACTS
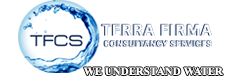
